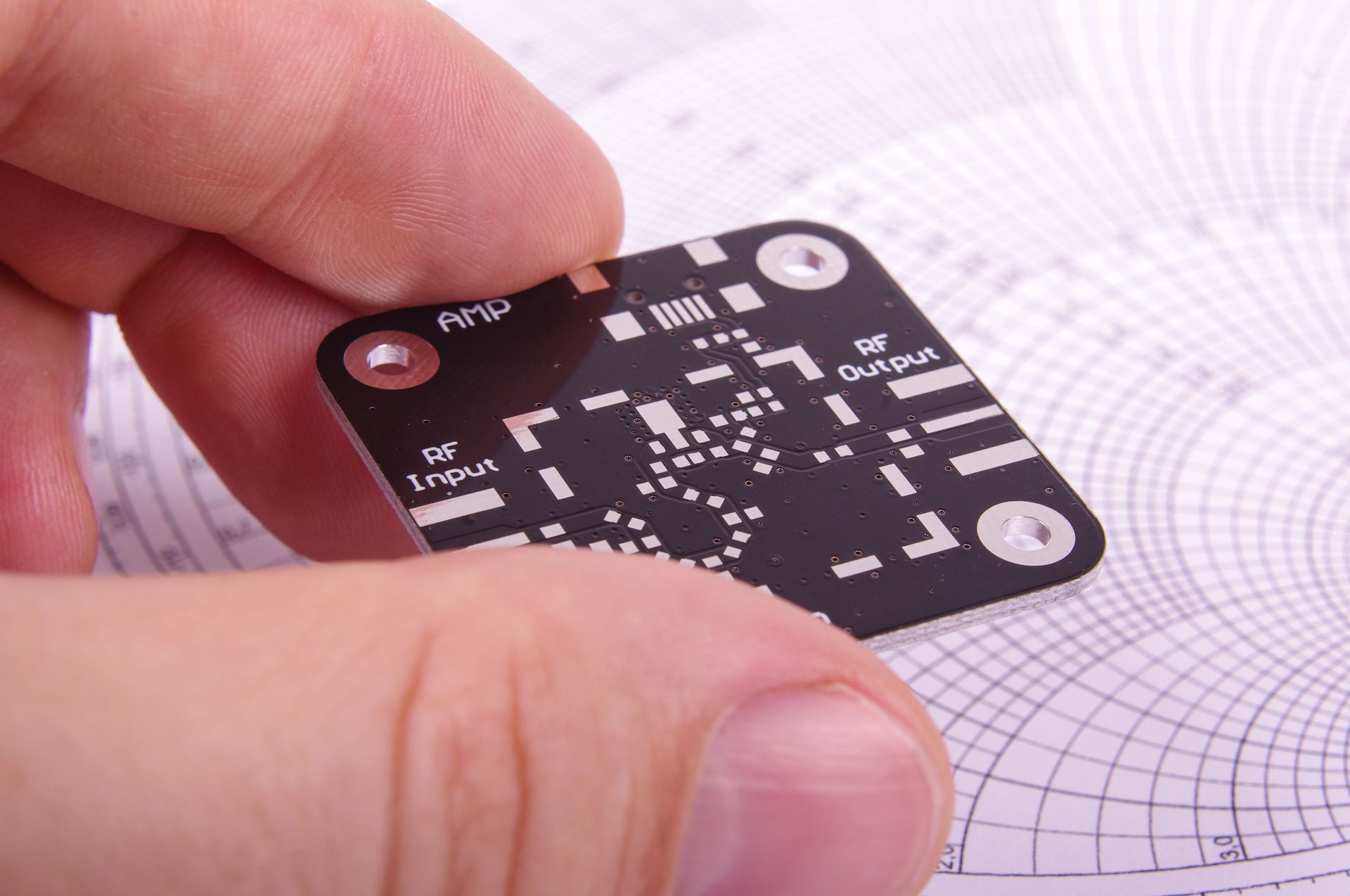
In the world of manufacturing, prototyping and small-scale production play crucial roles in the development and testing of new products. One popular method employed in these processes is vacuum casting. Vacuum casting offers several advantages that make it an attractive choice for both prototyping and small-scale production.
However, like any manufacturing technique, it also has its limitations. In this article, we will explore the advantages and limitations of vacuum casting in detail.
Advantages of Vacuum Casting
Here are five notable advantages of utilising vacuum casting.
Cost-effective prototyping
Vacuum casting enables the production of high-quality prototypes at a relatively low cost. Traditional methods like CNC machining or injection moulding can be expensive for producing a small number of prototypes. Vacuum casting eliminates the need for costly moulds and tooling, making it an economical option for prototyping.
Quick turnaround time
Vacuum casting allows for the rapid production of prototypes. With the absence of complex tooling, the
setup time is reduced, and multiple iterations of a design can be produced in a short span of time.
This feature is particularly advantageous when it comes to iterative design processes and meeting tight project deadlines.
Replication of complex geometries
Vacuum casting is well-suited for replicating intricate and complex geometries. The silicone moulds used in the process are highly flexible and can accurately capture fine details and undercuts that may be challenging to achieve with other manufacturing methods. This makes vacuum casting ideal for prototypes that require complex shapes or have intricate internal features.
Material versatility
Vacuum casting supports a wide range of materials, including various polyurethane resins with different mechanical properties, colours, and textures. This flexibility allows engineers and designers to simulate the properties of the final product closely. They can test factors such as strength, flexibility, transparency, and even the look and feel of the product.
Low-volume production
Besides prototyping, vacuum casting is also suitable for small-scale production runs. It offers a cost-effective solution for manufacturing limited quantities of parts without the need for expensive tooling or time-consuming setup processes. This is particularly advantageous for small businesses or startups that require small production batches to validate their product in the market.
Limitations of Vacuum Casting
Limitations of vacuum casting are outlined below.
Limited material options
While vacuum casting offers a range of polyurethane resins, it may not be suitable for certain applications that require specific material properties such as high-temperature resistance or biocompatibility.
In such cases, other manufacturing methods like injection moulding or
3D printing may be more appropriate.
Part size restrictions
Vacuum casting is most effective for producing small to medium-sized parts. Large parts may pose challenges due to limitations in the size of the silicone moulds and the overall process.
If a prototype or product requires large-scale production or oversized components, alternative manufacturing methods may need to be considered.
Longer production time for large quantities
While vacuum casting is efficient for small-scale production, it may not be the best choice for large quantities. The process involves creating silicone moulds for each part, which can be time-consuming and costly when scaled up.
Other methods like injection moulding may offer faster and more cost-effective production for larger volumes.
Limited surface finish options
Although vacuum casting can achieve excellent
surface finishes, it may not provide the same level of smoothness and precision as some other techniques, such as CNC machining.
Certain applications that require extremely smooth or highly detailed surfaces may need additional post-processing or alternative manufacturing methods.
Tooling wear and tear
Silicone moulds used in vacuum casting have a limited lifespan and can experience wear and tear over time, especially with
more complex geometries or abrasive materials.
Regular maintenance and replacement of moulds may be required, adding to the overall cost and time considerations.
M-Tek
At M-Tek Assembly we have decades of experience within the industry. We have accomplished a
net-zero carbon footprint by using electric vehicles, and for all PCBs we build, we plant a tree. Contact one of our SMT and PCB assembly experts today for assistance on anything regarding vacuum casting. Call
01189 455377 or follow us on
Twitter to stay up to date on our latest news.