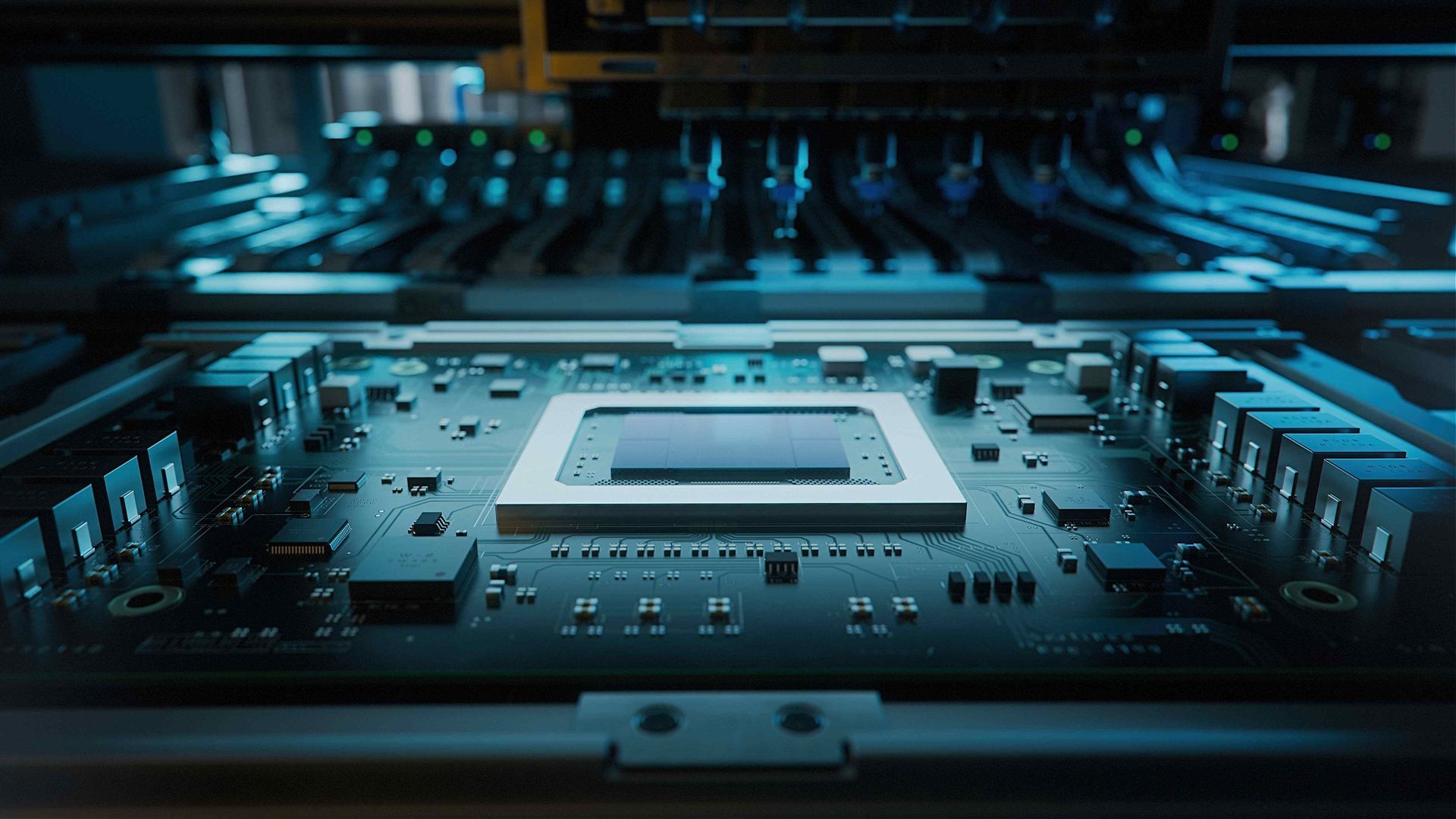
Vacuum casting is a widely used manufacturing process that involves creating high-quality replicas of a master pattern using a silicone mould. The process is highly versatile and cost-effective, making it an ideal solution for producing small to medium-sized production runs of complex parts. However, to achieve the desired results, it is crucial to invest in high-quality mould design.
What is Mould Design?
Mould design is creating a pattern or form for a mould, which is used to create a replica of the desired part. A well-designed mould is essential for the success of the vacuum casting process, as it ensures that the final product is accurate, consistent, and of high quality.
Advantages of Vacuum Casting in Mould Design
The most significant advantage of vacuum casting is its ability to produce highly detailed parts with complex geometries. However, achieving these complex shapes requires careful consideration and planning during the mould design process. The mould designer must consider factors such as part geometry, draft angles, wall thickness, and gate placement to ensure that the mould can produce a high-quality part.
Part geometry also plays a significant role in determining the complexity of the mould design. The designer must ensure that the mould can accurately capture the shape and features of the part, including undercuts and intricate details. To achieve this, the designer may use techniques such as split moulds or slides to create complex shapes that cannot be achieved with a single-part mould.
Draft angles are another critical consideration in mould design. Draft angles are the angles on the part's surface that allow it to be quickly released from the mould. Without sufficient draft angles, the position may become stuck in the mould, leading to damage or defects. The mould designer must carefully consider the part's geometry and draft angles to ensure that the part can be quickly released from the mould without causing any damage.
Wall thickness is also an essential factor in mould design. The designer must ensure that the mould's walls are thick enough to withstand the casting process's pressure and prevent deformation. At the same time, the walls must be thin enough to allow for efficient heat transfer during the casting process.
Gate placement is another crucial consideration in mould design. The gate is the point at which the molten material enters the mould. The designer must carefully consider the gate's size and location to ensure that the molten material can flow evenly through the mould, filling all cavities without creating air pockets or defects.
Other Considerations
In addition to the technical considerations mentioned above, the mould designer must also consider the type of material to be used in the casting process. Different materials have different properties, and the mould design must take these properties into account. For example, if the casting material is highly viscous, the designer may need to include additional gates or vents to ensure that the material can flow evenly through the mould.
Final Thoughts
The importance of mould design in vacuum casting cannot be overstated. A well-designed mould can significantly impact the quality and consistency of the final product. A poorly designed mould, on the other hand, can lead to defects, inaccuracies, and inconsistencies that can compromise the final product's integrity.
Investing in high-quality mould design is a critical step in ensuring the success of the vacuum casting process. This investment may require additional time and resources upfront, but it can save significant costs and headaches down the line by preventing defects, reducing waste, and improving overall quality.
M-Tek Assembly
We at M-Tek Assembly have years of experience in the field, and our group of knowledgeable engineers will help you every step of the way. Using M-Tek to repair printed circuit boards will also help the environment.
We have achieved a
net-zero carbon footprint by using electric vehicles, and for every circuit board we build, we plant a tree! Contact one of our SMT and PCB assembly experts today for assistance. Call
01189 455377 or follow us on
Twitter to learn more about our services, including vacuum casting.