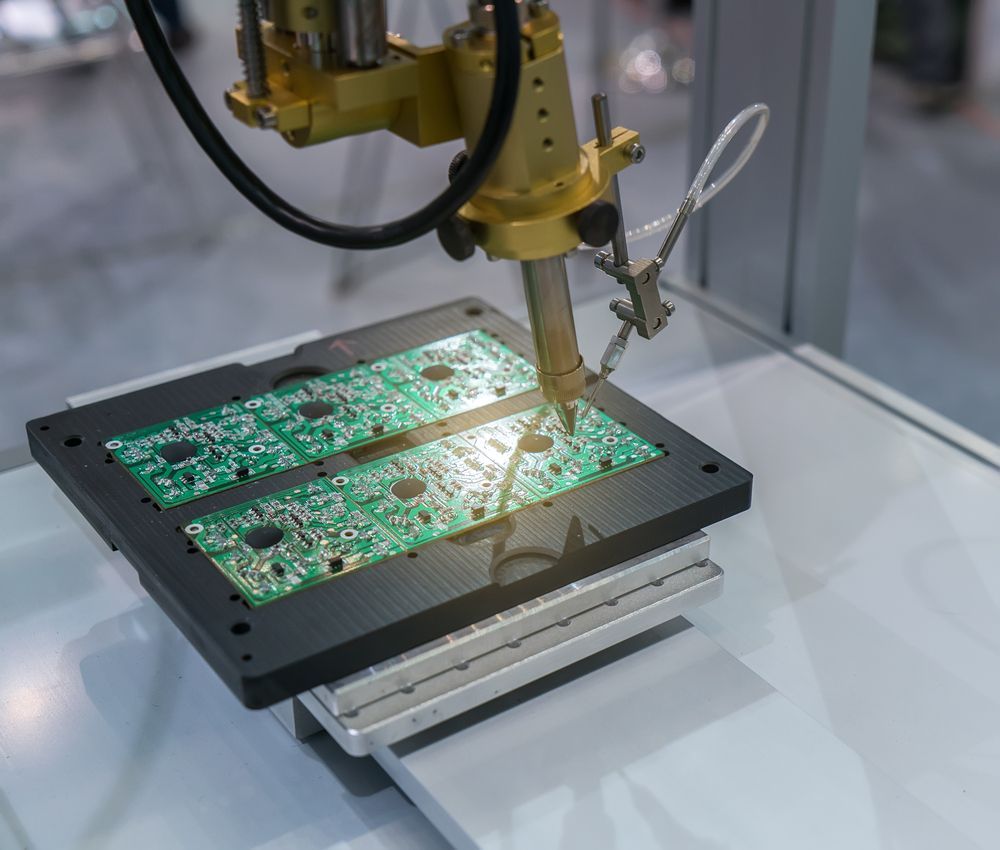
Printed Circuit Board (PCB) manufacturing plays a crucial role in the development and production of electronic devices.
The journey from the initial prototype stage to batch production is a critical transition that requires careful planning, optimisation, and attention to detail.
This article explores the key considerations and steps involved in transitioning from prototype to
batch production in PCB manufacturing.
Design for Manufacturing (DFM) Review
Before embarking on the transition, it is essential to conduct a comprehensive Design for Manufacturing (DFM) review. This review involves collaborating with the PCB manufacturer to evaluate the prototype design for any potential manufacturing issues.
The goal is to identify and resolve design elements that may cause challenges during batch production, such as component placement, trace routing, and spacing constraints.
Material Selection and Sourcing
Once the DFM review is complete, the next step is to assess the materials used in the prototype and evaluate their suitability for batch production.
During this stage, it is crucial to ensure the availability, reliability, and cost-effectiveness of the selected materials.
Collaborating closely with the PCB manufacturer can help identify alternative materials that meet the desired specifications while being readily available in larger quantities.
Component Procurement and Verification
In transitioning to batch production, it is necessary to establish a reliable supply chain for the required electronic components.
This involves identifying reputable component suppliers, negotiating favourable pricing and delivery terms, and verifying the authenticity of the components.
Counterfeit or substandard components can lead to production delays, quality issues, and product failures, making thorough verification essential.
Process Optimisation
To achieve efficient batch production, it is crucial to optimise the manufacturing processes. Collaborate with the PCB manufacturer to review and refine the production workflow, identifying areas for improvement, and streamlining the assembly and testing processes.
This may involve automation, equipment upgrades, and implementing quality control measures to ensure consistent and reliable production.
Prototyping to Pilot Run
Before commencing full-scale batch production, it is advisable to conduct a pilot run. This allows for a small-scale production run to validate the optimised processes, assess the quality of the manufactured boards, and identify any further refinements required.
The pilot run helps in identifying any unforeseen issues and ensures a smoother transition to larger batch production.
Testing and Quality Control
Implementing robust testing and quality control procedures is vital during the transition to batch production. Develop a comprehensive testing plan to verify the functionality and reliability of the PCBs at different stages of the production process.
This includes in-circuit testing, functional testing, and quality inspection to identify and rectify any defects or anomalies promptly.
Scalability and Production Capacity
Batch production involves producing PCBs in larger quantities, necessitating a careful evaluation of the manufacturing capacity.
Assess the scalability of the manufacturing processes and facilities to meet the desired production volumes while maintaining quality standards. This may involve increasing production lines, expanding the workforce, or optimising production scheduling for maximum efficiency.
Documentation and Collaboration
Throughout the transition, maintain clear and updated documentation of the design, manufacturing processes, and quality control procedures.
Effective collaboration between the design team, PCB manufacturer, and other stakeholders is crucial to ensure a smooth transition.
Regular communication and feedback exchanges help address any challenges and facilitate a successful transition to batch production.
Continuous Improvement
Transitioning from prototype to batch production is not a one-time event but an ongoing process. Embrace a culture of continuous improvement, where feedback from the manufacturing process is collected, analysed, and used to refine and optimise the PCB design and production.
By learning from each production batch, you can enhance efficiency, quality, and cost-effectiveness over time.
Final Thoughts
In conclusion, transitioning from prototype to batch production in PCB manufacturing requires a systematic approach, collaboration, and attention to detail.
By conducting a thorough DFM review, optimising processes, ensuring reliable material sourcing, implementing rigorous testing and quality control measures, and fostering continuous improvement, you can successfully scale up production while maintaining high-quality standards.
The transition to batch production is a significant milestone that paves the way for the efficient and cost-effective manufacturing of electronic devices.
M-Tek
At M-Tek Assembly we have decades of experience. We have accomplished a
net-zero carbon footprint by using electric vehicles, and for all PCBs we build, we plant a tree. Contact us today for guidance on anything regarding PCBs and rapid prototyping. Call
01189 455377 or follow us on
Twitter to learn more about our products and services.