How Vacuum Casting Enables Complex Part Reproduction for Medical Devices
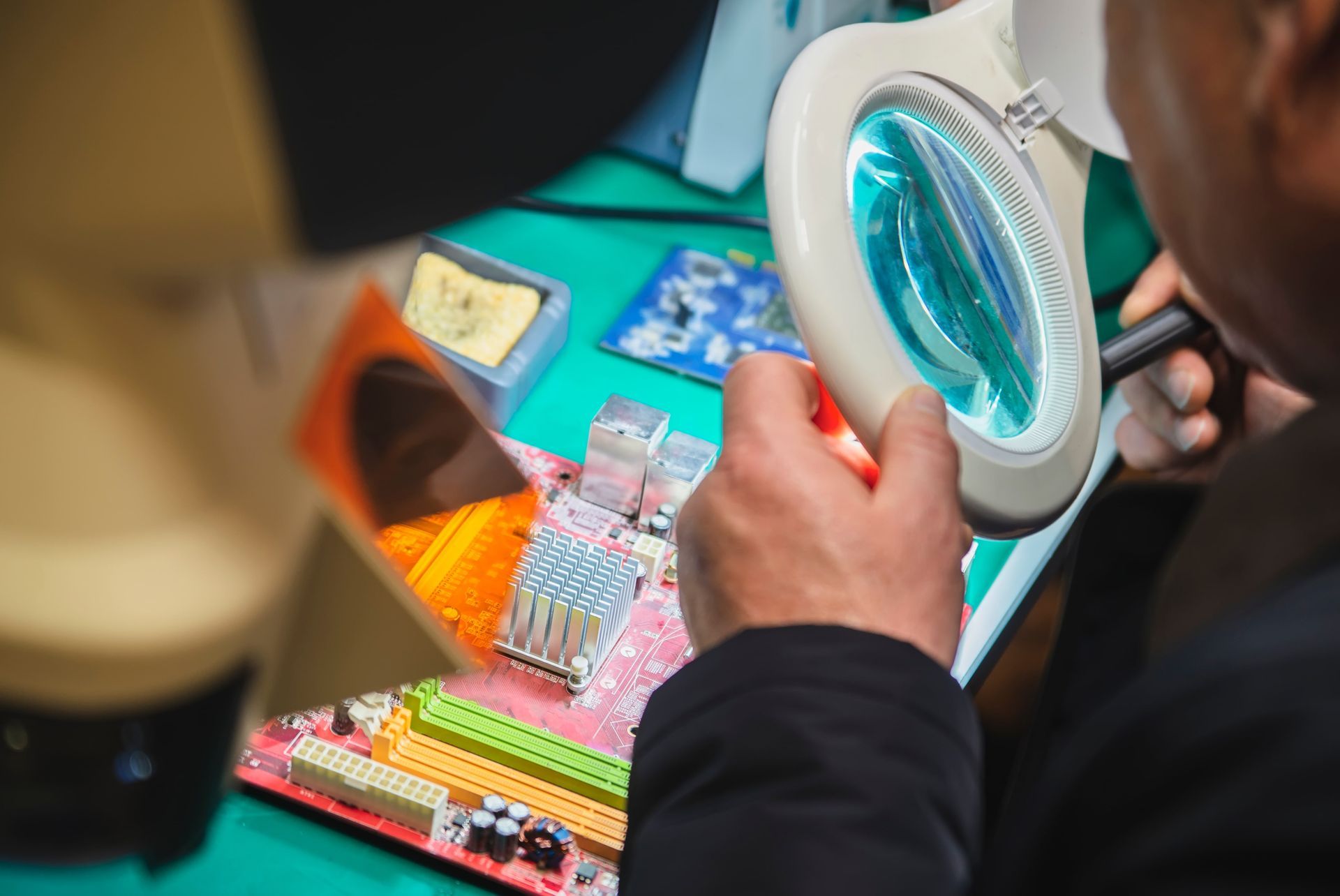
Medical devices play a crucial role in modern healthcare, ranging from surgical instruments to implants and prosthetics. Many of these devices require complex parts with intricate geometries that are challenging to produce using traditional manufacturing methods. However, vacuum casting has emerged as a powerful and versatile technique that enables the reproduction of complex parts for medical devices with high precision and accuracy.
Benefits of Vacuum Casting For Medical Devices
One of the key advantages of vacuum casting for medical devices is its ability to reproduce complex parts with high fidelity. Medical devices often require intricate geometries and fine features, such as thin walls, overhangs, and undercuts, which are challenging to achieve using traditional manufacturing methods like machining or injection moulding. Vacuum casting can reproduce these complex features accurately, making it ideal for producing functional prototypes, pre-production parts, and low-volume production runs of medical devices.
Another significant benefit of vacuum casting for medical devices is its
versatility in material selection. Polyurethane resins used in vacuum casting come in a wide range of formulations, offering varying levels of mechanical properties, biocompatibility, and chemical resistance. This allows medical device manufacturers to choose a material that meets the specific requirements of their application, whether it's for surgical instruments, implants, or prosthetics.
Vacuum casting also offers
cost-effective solutions for medical device production. Traditional manufacturing methods like machining or injection moulding often require expensive tooling or moulds, which can be prohibitive for small production runs or prototyping. Vacuum casting, on the other hand, utilises relatively inexpensive silicone moulds that can be produced quickly and easily from a 3D printed or CNC-machined master pattern.
Furthermore, vacuum casting allows for rapid production cycles. Silicone moulds used in vacuum casting are durable and can produce multiple parts with high accuracy and consistency. This means that medical device manufacturers can iterate and refine their designs quickly without incurring additional tooling costs.
Final Thoughts
In conclusion, vacuum casting is a powerful and versatile manufacturing process that enables the reproduction of complex parts for medical devices. Vacuum casting has revolutionised the production of medical devices, allowing for the creation of functional prototypes, pre-production parts, and low-volume production runs with high precision, accuracy, and efficiency.
M-Tek Assembly
At M-Tek Assembly we have decades of experience in the field. We have achieved a net-zero carbon footprint by using EVs, and for every PCB we build, we plant a tree!
Contact one of our SMT and PCB assembly experts today for assistance. Call 01189 455377 or follow us on Twitter to learn more about our services, including vacuum casting.