Both vacuum casting and injection moulding are excellent techniques. Both are frequently used in the prototyping industry, and each provides a particular set of benefits. It can be challenging to decide between the two, though, because the procedures are similar in several ways (both are excellent for plastic components; both employ a mould with a hollow to produce parts, etc.).
There are some elements that one can take into consideration while making a decision, even though it is frequently advisable to consult an expert like M-Tek for specialised guidance on which manufacturing technique is most suitable for a given project. The easiest method to decide whether injection moulding or vacuum casting is the appropriate process for your project is to become familiar with these aspects.
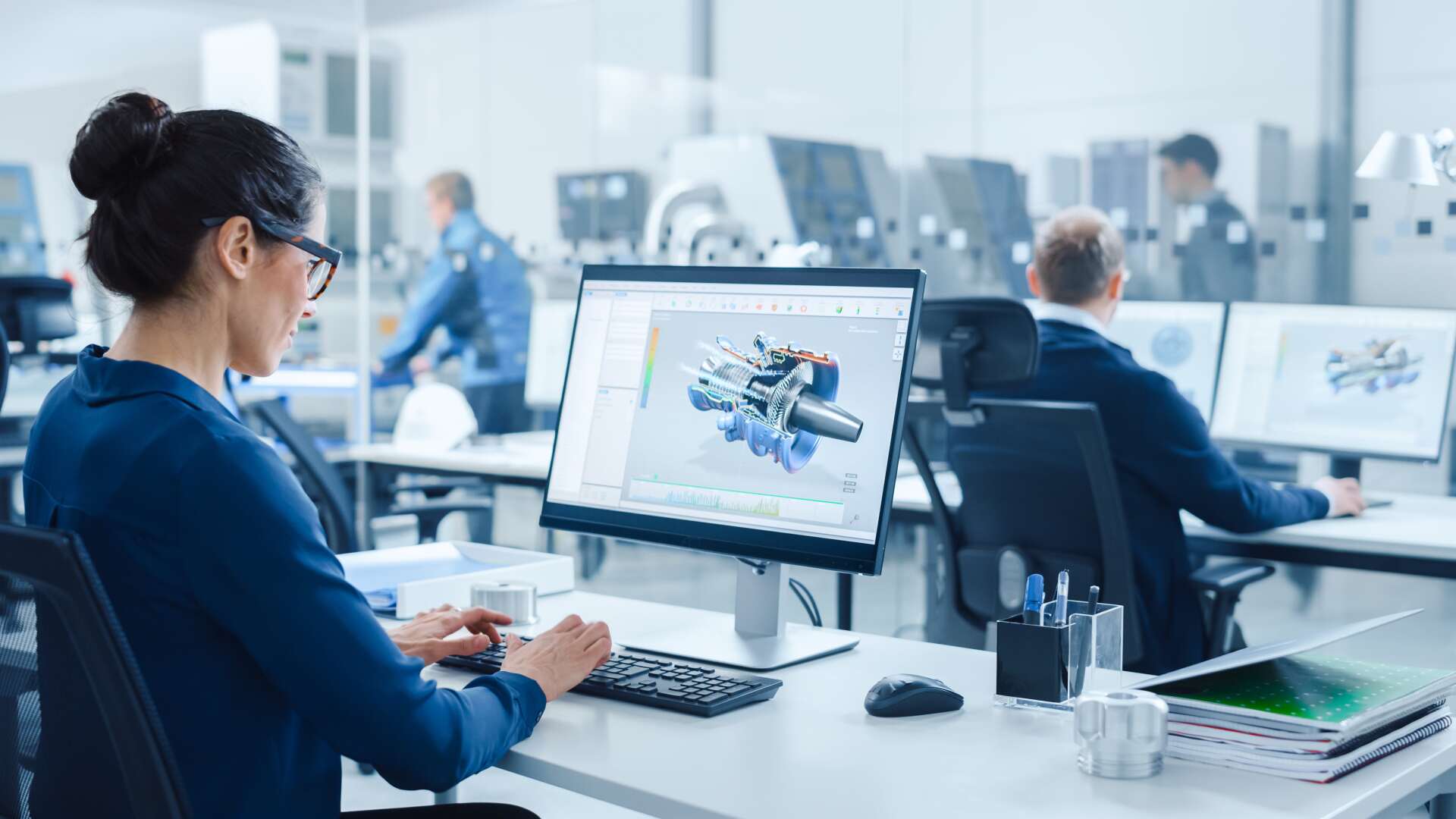
What is Vacuum Casting?
Vacuum casting is an intriguing substitute for injection moulding that can be utilised to produce small numbers of a product affordably while being less popular. A master model, which is made using CNC equipment, is the first step in the vacuum casting process. 3D printing is another option. After being submerged in liquid silicone, the master model is then dried, sliced, and separated from it.
Once the silicone has dried, it can be used as a mould. The silicone mould is filled with casting resin, which the vacuum removes to guarantee a flawless finish. The silicone mould, which can be used about 20 times, is used to remove the resin component after it has dried.
What is Injection Moulding?
The molten material is poured into a mould during the commonly used manufacturing technique known as injection moulding. Large numbers of parts may be produced with it and employed in sectors like healthcare and consumer goods. You'll probably be seated close to an injection-moulded component.
In the course of the injection moulding procedure, ingredients, occasionally multiple materials, are heated and mixed in a barrel. The substance is melted, pressed into a mould, and allowed to cool while taking on the shape of the mould's interior. The mould can be used to create numerous identical pieces by repeatedly doing this procedure.
Although injection moulding is typically associated with production, it is also practical for prototypes. This is partly because of rapid tooling, a technique for swiftly and affordably producing prototype injection moulds. However, due to the high cost of even quick tooling, injection moulding is not recommended for parts that need to be produced in extremely small quantities.
When is Injection Moulding more Appropriate than Vacuum Casting?
Many companies might not even consider the vacuum casting process for their items because injection moulding is more frequently used than vacuum casting. However, there are some circumstances when the silicone-based method offers greater value and perhaps even superior quality.
Quantity
It is difficult to consider any other option besides injection moulding for very large volumes of parts. Even with the use of quick tooling, the setup costs for injection moulding are considerable, but the unit costs are quite low. This indicates that the initial investment in the setup is easily recovered through savings on each unit when a corporation needs hundreds or thousands of copies of an item.
On the other hand, not every business needs a large number of duplicates of a part. Vacuum casting may be a preferable option if only a few to one hundred parts need to be produced because the setup costs are so much lower.
Quality
Injection moulding enables the production of more intricate parts than vacuum casting since its tooling is typically composed of premium metals. For extremely intricate products, injection moulding may consequently be the preferable choice.
Vacuum casting may be preferable for simpler components, especially those that only need to be produced in small quantities. Vacuum casting is not just a low-cost choice, though; it can provide an incredibly smooth surface finish, which means even simple parts may look nicer when created using vacuum casting.
Importantly, making moulds for vacuum casting is a quicker process than making equipment for injection moulding, therefore vacuum casting is frequently a preferable option for time-sensitive prototyping work for extremely small numbers. (For bigger volumes, injection moulding will be faster.)
Speed
Positive ripple effects result from vacuum casting's minimal startup costs. Vacuum casting moulds may be changed far more easily and affordably than injection moulding tooling if a design needs to be changed at any point during production.
This often means that during the first stages of development, vacuum casting is frequently the better option. Enterprises frequently employ vacuum casting to produce early prototypes before adopting injection moulding to produce final products or later-stage prototypes.
Fill in our online form here for more information on vacuum casting. Or, call us on 01189 455377 and speak to one of our PCB experts today.
Follow us on
Twitter to stay up to date with our services.
For more information on the vacuum casting process,
read our previous blog here.