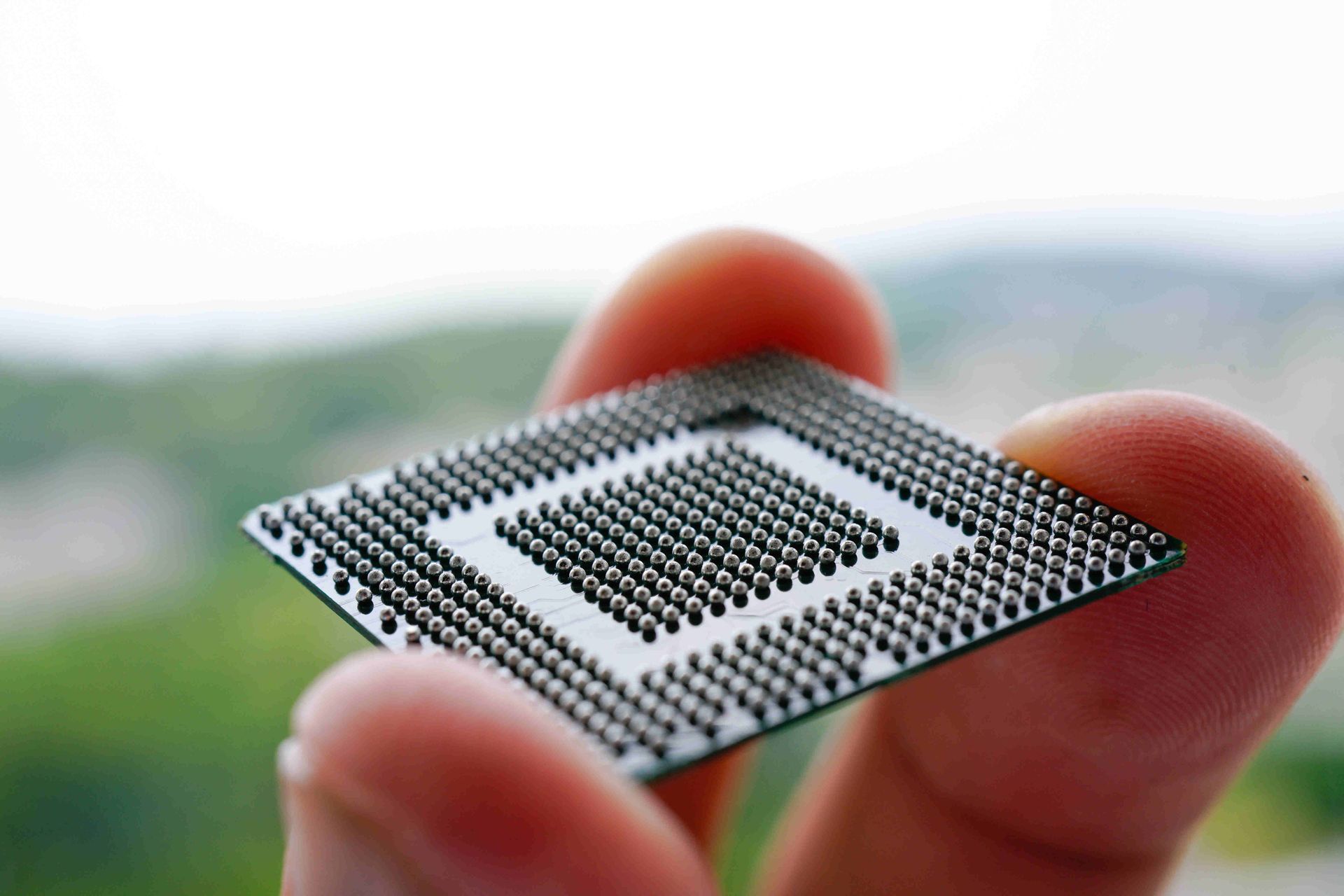
Ball Grid Array (BGA) packaging has become widely popular in the electronics industry due to its numerous advantages such as higher component density, improved thermal performance, and reduced signal inductance.
However, like any other electronic component, BGAs are not immune to failures. Understanding the causes of BGA failures, detecting them early, and implementing effective prevention strategies are essential for ensuring the reliability and performance of electronic devices.
In this article, we will delve into the world of BGA failure analysis and explore the causes, detection methods, and prevention strategies associated with it.
Causes of BGA Failures
Listed below are the causes of BGA failures.
Thermal Stress
One of the primary causes of BGA failures is thermal stress. When electronic devices undergo temperature cycling or experience uneven heating/cooling, the resulting expansion and contraction of materials can lead to mechanical stresses on the BGA package.
Over time, these stresses can cause cracks in the solder joints or delamination within the
BGA, leading to electrical failures.
Insufficient Soldering
Poor soldering during the assembly process can also contribute to BGA failures. Insufficient solder paste, improper reflow profiles, or inadequate solder wetting can result in weak solder joints, causing intermittent connections, shorts, or openings.
Mechanical Shock and Vibration
Excessive mechanical shock and vibration can cause mechanical stress on the BGA package, leading to cracked solder joints or even detachment of the BGA from the PCB. This can result in electrical discontinuities and failures.
Contamination and Corrosion: Contaminants, such as flux residues or moisture, can affect the long-term reliability of BGAs. Corrosion caused by moisture ingress or the presence of corrosive substances can deteriorate the solder joints and lead to failures.
Detection of BGA Failures
How to detect BGA failures is listed below.
X-ray Inspection
X-ray inspection is a commonly used non-destructive testing method for detecting BGA failures. It allows for the visualisation of internal structures and solder joints, making it possible to identify issues like voids, cracks, or insufficient solder volume.
Optical Inspection
The
optical inspection involves using microscopes or cameras to examine the external surface of BGAs. It helps detect visible defects such as misalignment, cracks, or solder ball deformities. Optical inspection can be performed manually or automated using machine vision systems.
Electrical Testing
Electrical testing, such as continuity checks and functional testing, can reveal open circuits, shorts, or intermittent connections in BGAs. These tests are usually performed using specialised test equipment, such as boundary scan testers or in-circuit testers.
Prevention Strategies
Listed below are prevention strategies for BGAs.
Design Optimisation
Proper BGA design is crucial for ensuring long-term reliability. Factors such as component layout, pad geometry, and via placement should be carefully considered to minimise thermal stress and optimise signal integrity.
Assembly Process Control
Implementing robust assembly processes is essential to prevent BGA failures. This includes proper solder paste application, optimised reflow profiles, and adequate inspection and testing during assembly.
Additionally, using automated equipment and advanced technologies, such as solder paste inspection systems, can improve process control and minimise human error.
Thermal Management
Efficient thermal management is crucial for mitigating thermal stress on BGAs. Proper heat sinking, thermal vias, and adequate airflow or heat dissipation mechanisms should be incorporated into the design to prevent excessive temperature gradients.
Quality Control and Testing
Regular quality control checks and testing throughout the manufacturing process can help identify potential BGA failures early on. This includes visual inspection, X-ray inspection, electrical testing, and reliability testing such as temperature cycling or mechanical shock tests.
M-Tek
At M-Tek Assembly we have years of experience within the industry. We have achieved a
net-zero carbon footprint by using electric vehicles, and for all PCB and BGAs we build, we plant a tree. Contact one of our SMT and PCB assembly experts today for assistance. Call
01189 455377 or follow us on
Twitter to learn more about our products and services.