FAQs on Vacuum Casting
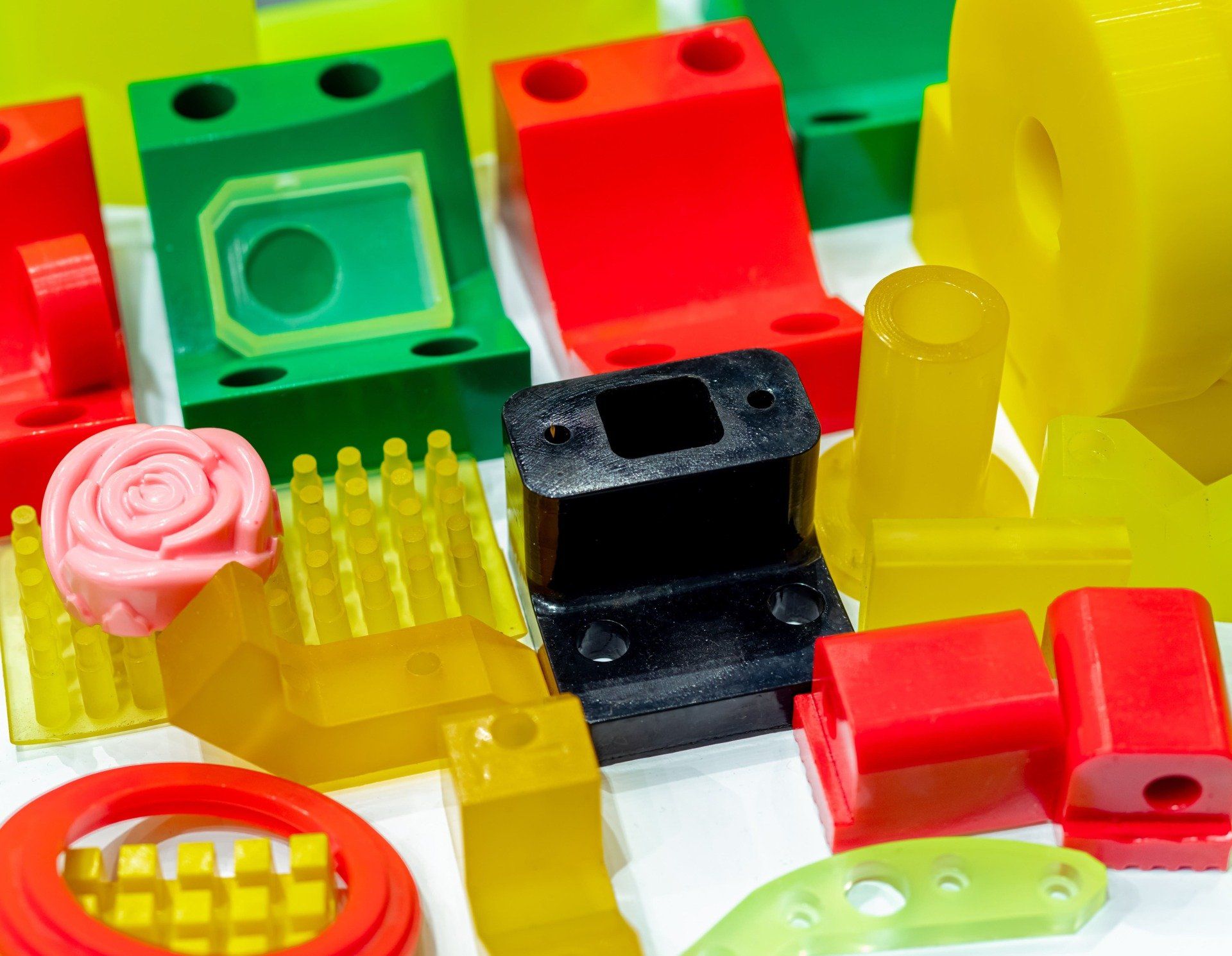
At M-TEK, our specialists are experts in the contract electronic industry and undergo several different procedures for our vast clientele. That includes vacuum casting for certain industries and high-end businesses.
But, what exactly is vacuum casting? We’re here to break down the most frequently asked questions on the subject and how M-Tek Assembly can help.
What is Vacuum Casting?
Also known as polyurethane or urethane casting, the vacuum casting process involves utilising a vacuum to draw a liquid substance into a silicone mould in order to produce complex components. It is used when air entrapment has become an obstacle within the mould. Elastomers such as rubber and plastic are employed as liquids in vacuum casting.
Since vacuum casting has a lower production cost than injection moulding, it is a more affordable option for producing plastic components. For batch production and other low-volume production tasks, vacuum casting is a great production method. Vacuum casting is widely utilised in the production of consumer goods, FMCGs, and industrial electronics.
How Does Vacuum Casting Work?
Injection moulding, where the cast material is injected into moulds to create objects, is very similar to vacuum casting. However, the types of moulds used to produce each process—vacuum casting and injection moulding—are different.
Moulds used in injection moulding can be produced from steel, aluminium, etc. On the other side, silicone moulds are employed in vacuum casting. This significantly lowers the cost of producing moulds because silicone is less expensive and has good endurance.
Polyurethane is the material that is most frequently utilised in vacuum casting. Good structural strength, elasticity, flexibility, shock and temperature resistance, among other qualities, are all characteristics of distinct polyurethanes. Different polyurethanes might therefore be utilised, depending on the sort of product being created.
For more information on the vacuum casting process,
read our previous blog here.
When is Vacuum Casting Used?
Prototypes and finished parts can both be made using vacuum casting. It can be used to create concept models, visual prototypes, functional test prototypes, pre-production prototypes, models for testing air and heat flow, and assembly line trials.
Vacuum casting works well for functional prototypes when over-moulding metal parts or adding elastomeric sealing elements to pieces created by other prototyping techniques. Polyurethane is adequately durable for end-use items, such as elastomeric seals, over-moulded ergonomic grips, or complex geometries.
Industries as diverse as medical, life science, automotive, aerospace, and general manufacturing utilise the vacuum casting process.
What is Vacuum Casting Used For?
In contrast to the conventional injection moulding process, vacuum casting is a very effective and economical method for creating elaborate and complex goods. Due to the effectiveness of the production process, vacuum casting is widely employed in the fabrication of commercial products.
That’s why vacuum casting is utilised in consumer products such as sunglasses, pens and combs. They are also great in the food and beverage industry, creating packaging products such as food containers, mugs and glasses.
What Are the Benefits?
At M-Tek, we understand the various benefits that vacuum casting can have on the manufacturing process. It speeds up the production of intricate shapes, with the clearest line of precision. All at a lower cost as well. Benefits also include:
Complex and elaborate shapes can be produced with high accuracy and ease.- Polyurethane cost is low, therefore vacuum casting is cost-effective.
- Metal moulds are more difficult to produce than silicone moulds.
M-Tek Assembly
Established in 1996, M-TEK Assembly creates and manufactures printed circuit boards throughout the UK. Supplying to a variety of industries, PCB assembly has many benefits and we ensure that the manufacturing process runs smoothly and efficiently.
Fill in our online form here for more information on vacuum casting. Or, call us on 01189 455377 and speak to one of our PCB experts today.